Acid Washing Bricks
But to our dismay, the mouldings company changed their mind -- after the mouldings were up, they said we should have washed the bricks first, as the acid would damage the mouldings. So we had to buy A$500 of a sealing product to protect our mouldings (it's a suspension of silicone in a solvent, so it doesn't change the appearance after application). It work very well in the end.
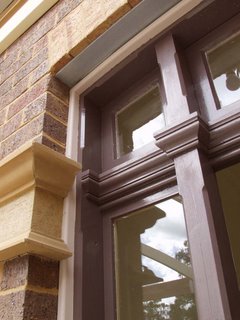
The current fashion amongst brick-cleaners is to use a high-pressure spray of sulphuric acid, diluted 1 part acid to 8 parts water. But this would pose another risk to our mouldings, and it can remove too much mortar.
We opted to have the acid applied with a brush (1 part acid to 4 parts water). Then it was left for about 30 minutes, and washed down with a low-pressure spray. We were thrilled with the reuslt, as we had grown used to looking at un-washed walls for about 6 months!