Wednesday, January 25, 2006
Tuesday, January 03, 2006
Security System
Before we start moving anything into the house in the way of appliances or furniture, we have installed and commissioned a security system (Sierra, now owned by Honeywell). I did the installation, as I have an electrical engineering background. But it has taken me about 5 days all up to complete the job.
before it was finallycommissioned, I was worried that the security system itslef could be stolen, as it was the most valuable item in the house for about a week.
We have dual-detetcion motion sensors in seven rooms, plus magentic reed-switches on external doors and selected windows. The motion detectors have both a micro-wave and passive-infra-red systems for detecting people-movement (thus increasing the reliability, and reducing false-detections). A remote control is the only of interest. Other than that, its probably a standard alarm system.
before it was finallycommissioned, I was worried that the security system itslef could be stolen, as it was the most valuable item in the house for about a week.
We have dual-detetcion motion sensors in seven rooms, plus magentic reed-switches on external doors and selected windows. The motion detectors have both a micro-wave and passive-infra-red systems for detecting people-movement (thus increasing the reliability, and reducing false-detections). A remote control is the only of interest. Other than that, its probably a standard alarm system.
Decorative plaster
After "hanging" the plasterboard, the next stage is "stopping-up" the joins and corners. This work started around late November.
Our plasterer, Amore, liked to complete the work in each area as he went, rather than stop-up the whole house first, and then do the decorative.
We chose to put "bull-nosing" on many of the external corners in the house. This is a good idea aethetically, but they were quite tedious for Amore to fit, as they were not made as a perfect right-angle in shape - so it was quite a juggle to fit them.
Our plasterer, Amore, liked to complete the work in each area as he went, rather than stop-up the whole house first, and then do the decorative.
We chose to put "bull-nosing" on many of the external corners in the house. This is a good idea aethetically, but they were quite tedious for Amore to fit, as they were not made as a perfect right-angle in shape - so it was quite a juggle to fit them.
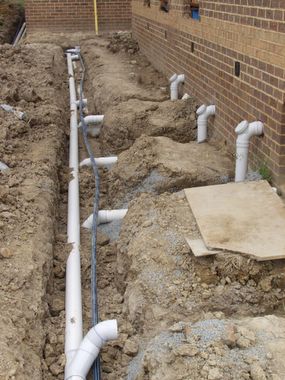
Three drains in one trench - the potable stormwater drain is on top (in 100mm PVC fro strength, even though 90 mm is permitted). Underneath is the sewer and also the surface/sub-surface drainage. Note :- the grey water from the house (excluding kitchen sullage) is kept separate from other drains in the house until it joins the sewer main line - this allows me to easily re-direct gray-water for recycling at a later date.
Drains
All our internal plumbing was roughed-in, but we had no drains to connect it to. Fotunately, I had slected a plumber who can do both inmternal and external plumbing (some plmbers specialised in only one).
Onece again, the energy-certiciation system required for new homes in Australia had an impact here. As part of our energy certification, we had to have rain-water recycling (or solar energy assisted heated water supply). I chose to have rain-water recycling. So this means we have three types of external drains:
1) "Potable" rainwater from roof-areas only
2) Surface water collection and sub-surface cut-ff drains
3) Sewer
All-up, this amounted to about 400 metres of drains, circum-naviagating the house. Cost was around A$1000 (US$7000).
The rainwater system doesn't have the collection sump, or sump-pump installed yet, but we allowed a space for it in the layout of the system.
My electrician also installed the power-feed for the rainwater-sump-pump, and sewer-sump-pump at this time (our off-site sewer is not a gravity system, instead it is a pressure sewer get the stuff up the hill near us).
Onece again, the energy-certiciation system required for new homes in Australia had an impact here. As part of our energy certification, we had to have rain-water recycling (or solar energy assisted heated water supply). I chose to have rain-water recycling. So this means we have three types of external drains:
1) "Potable" rainwater from roof-areas only
2) Surface water collection and sub-surface cut-ff drains
3) Sewer
All-up, this amounted to about 400 metres of drains, circum-naviagating the house. Cost was around A$1000 (US$7000).
The rainwater system doesn't have the collection sump, or sump-pump installed yet, but we allowed a space for it in the layout of the system.
My electrician also installed the power-feed for the rainwater-sump-pump, and sewer-sump-pump at this time (our off-site sewer is not a gravity system, instead it is a pressure sewer get the stuff up the hill near us).
More Excavation Work
I don't currently have a photo to depict this, but also in November, we had some more excavation work down, and the old original timber garage rewmoved (which we hd been using for storage on-site). The excavation work was done on the high-side of the slope, where the house appeared too "dug-in" to the gound. We removed lots of earth, to open this area up, and placed removed earth around on the low-side to give us a larger flat area for entertaining.
Plasterboard Hangers
The plasterboard hangers were scheduled for early November, but I had to delay them by one-week when I realised that I was not going to have the frame ready for them.
So the plasterboard was installed by a team of three "hangers" around November 10. They took three days to do it (they said thyy would have taken two days on a normal house, but our 12-foot ceilings slowed them down).
They did a great job, and put all the off-cuts into a bin that I had arranged for them.
So the plasterboard was installed by a team of three "hangers" around November 10. They took three days to do it (they said thyy would have taken two days on a normal house, but our 12-foot ceilings slowed them down).
They did a great job, and put all the off-cuts into a bin that I had arranged for them.
Stuff-Ups - We Do Have Them
Stuff ups are different when you make them yourself - and we have made some on this project. You can't get mad, or even, because its your fault when you are owner-builder. In the case of our kitchen window, I didn't listen to Julie properly, and so I had a kitchen window made that had a 175mm splash-back underneath it, where the kitchen sink was to be.
After the window was fitted, Julie looked at it and said it was wrong. I said "no it isn't, its what was in the design drawing". But then Julie showed me a photo of how she thought it would be, and then I realised my mistake.
We lived with the window installed for about 3 weeks, before we both decied we couldn't live with it any longer, and so it went back to the joinery to be modified. The top part (radiusesd head, and hopper-sashes) was retained, new casement sashes and styles were fitted, and the sill was retained. This modification cost over A$1000 (US$700), but it really was worth it.
After the window was fitted, Julie looked at it and said it was wrong. I said "no it isn't, its what was in the design drawing". But then Julie showed me a photo of how she thought it would be, and then I realised my mistake.
We lived with the window installed for about 3 weeks, before we both decied we couldn't live with it any longer, and so it went back to the joinery to be modified. The top part (radiusesd head, and hopper-sashes) was retained, new casement sashes and styles were fitted, and the sill was retained. This modification cost over A$1000 (US$700), but it really was worth it.
Wall Insulation & Energy Ratings
All external walls were insulated in R2 polyester (fire rated) batts. These are white in colour. All new homes in Australia must now achieve a 5-Star energy certification, which usually implies full insulation,and careful design of windows, shade-control, and aspect.
We also fitted some acoustic insulation to some internal walls to provide better isolation between rooms (e.g. kitchen/bedroom wall, and bathroom/bedroom wall). This is also polyester, but much denser than the white thermal insulation.
We also fitted some acoustic insulation to some internal walls to provide better isolation between rooms (e.g. kitchen/bedroom wall, and bathroom/bedroom wall). This is also polyester, but much denser than the white thermal insulation.
Completing the Plumbing and Electrical "Rough-In"
Also as part of the frame preparation process, I had my electrician and plumber finish off the rough-in.
Its a good idea to take photos off all the walls after the rough-in work is complete. This way you can used the photos later if you need to locate plumbing, wires, or wall-studs.
Its a good idea to take photos off all the walls after the rough-in work is complete. This way you can used the photos later if you need to locate plumbing, wires, or wall-studs.
Getting the Frame Ready for Plastering
Before plastering the internal walls, I had a list a mile long of all the things that needed doing. For example:
* Extra noggins to allow for fixing of things like: toilet roll holders, wardrobe frames, light fittings, etc.
* Bell-wires for front door bells, and servants-bells (NOW HANG ON - we DO NOT have servants, but I did buy an old Edwardian room-indicator panel (for about US$20), so that the maid can see which room is requesting service, and I am keen to install it and get it running).
* TV, phone, computer and security system wiring.
* Straighten the frame in corners, and replace a few warped studs.
* Install wall & ceiling insulation
* Install lights in the roof space
* etc, etc, etc.....
The "frame preparation" process went on for about 6 weeks or. It was slow, as I decided to do this work myslef, instead of getting trades to do it. Cost was another issue here, especially with work that I can do myself.
* Extra noggins to allow for fixing of things like: toilet roll holders, wardrobe frames, light fittings, etc.
* Bell-wires for front door bells, and servants-bells (NOW HANG ON - we DO NOT have servants, but I did buy an old Edwardian room-indicator panel (for about US$20), so that the maid can see which room is requesting service, and I am keen to install it and get it running).
* TV, phone, computer and security system wiring.
* Straighten the frame in corners, and replace a few warped studs.
* Install wall & ceiling insulation
* Install lights in the roof space
* etc, etc, etc.....
The "frame preparation" process went on for about 6 weeks or. It was slow, as I decided to do this work myslef, instead of getting trades to do it. Cost was another issue here, especially with work that I can do myself.